Construct a Solid, Squeak-Free Floor System
If not installed properly, floor systems can squeak, buckle, and cause nail-pop. To cut callbacks due to these problems, APA recommends a glued floor system, following the simple construction steps below.
Step 1: Choose the correct materials, including dry materials such as engineered wood or dry lumber.
Dry lumber is more dimensionally stable than green lumber. As it dries, green dimension lumber tends to cause nail-pop, making bumps under the finish flooring. These bumps can lead to squeaks and to accelerated wear of the finish flooring. Engineered wood, on the other hand, is dried during production and should not cause nail-pop when properly installed.
APA structural panels are manufactured in a variety of grades and thicknesses. When selecting your floor panel, consider the applied load, joist spacing, finish flooring and floor system (e.g., single floor or subflooring plus underlayment). See Table 1 to select the panel that is best for your job.
Step 2: 1/8" Panel spacing is recommended, leaving room for expansion due to changes in moisture content.

From their initial mill-dry state, panels will expand as they reach their equilibrium moisture content. If they are installed without room to expand, panels may buckle. APA recommends leaving 1/8-inch space at time of installation for all sheathing and Sturd-I-Floor edge and end joints, including tongue-and-groove joints, unless recommended otherwise by the product manufacturer.
To further minimize the potential for panel buckling, allow panels to acclimatize prior to installation. To do this, stand panels on edge for several days, allowing air circulation to all sides.
Step 3: If using a glued floor system, select an adhesive conforming to APA Performance Specification AFG-01 or ASTM D3498.
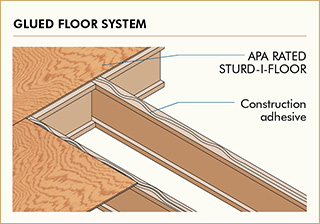
To prevent premature dryout of the adhesive, spread enough glue to lay ONLY one or two panels at a time. To assure the panels will be firmly and permanently secured to the joists, wipe away water, dust and debris before applying glue.
Apply glue (about 1/4-inch-diameter bead) to framing members in a continuous line or in a serpentine pattern on wide areas. Glue all tongue-and-groove joints by spreading glue in groove. Avoid squeeze-out by applying a thinner line in groove (about 1/8 inch) than on joists.
Complete all nailing of each panel before the glue sets or skins over. Check glue manufacturer's recommendations for allowable time. Remember, warm weather accelerates glue setting.
Step 4: Nail panels correctly to prevent squeaks.
The correct nail size and spacing for your job depends on your joist spacing and panel thickness, as well as the type of panel product you are using. Attachment schedules and fastener recommendations are provided in Table 1.
For other structural wood panel application recommendations and typical panel trademarks, see APA's Engineered Wood Construction Guide, Form E30.
Table 1: Panel and Attachment RecommendationsWe have field representatives in many major U.S. cities and in Canada who can help answer questions involving APA trademarked products. For additional assistance in specifying engineered wood products, contact us:
APA HEADQUARTERS: 7011 South 19th Street, Tacoma, Washington 98466 • (253) 565-6600 • Fax: (253) 565-7265
APA PRODUCT SUPPORT HELP DESK: (253) 620-7400 • E-mail: help@apawood.org
Disclaimer: The information contained herein is based on APA – The Engineered Wood Association's continuing programs of laboratory testing, product research, and comprehensive field experience. Neither APA, nor its members make any warranty, expressed or implied, or assume any legal liability or responsibility for the use, application of, and/or reference to opinions, findings, conclusions, or recommendations included in this publication. Consult your local jurisdiction or design professional to assure compliance with code, construction and performance requirements. Because APA has no control over quality of workmanship or the conditions under which engineered wood products are used, it cannot accept responsibility for product performance or designs as actually constructed.
Form No. Q300/July 2016
© 2016 APA – The Engineered Wood Association. All Rights Reserved.